Polidoro estende NET@PRO a misurazione produttività e manutenzione
L’AZIENDA
Polidoro nasce a Schio nel 1945 per opera di Aldo Polidoro e del fratello Silvio, che fin da subito accendono un futuro luminoso iniziando con la produzione di beccucci ad acetilene per l’illuminazione.
Successivamente Polidoro passa alla produzione di isolatori elettrici in ceramica. Nel 1955, grazie alla ricerca continua di soluzioni innovative che contraddistingue Polidoro, nasce la stufa Radiantgas a gas liquido, la quale riscontra un notevole successo di mercato.
Ancora una volta Polidoro si dimostra un’azienda capace di leggere il futuro e cogliere le opportunità che questo offre. Con la scoperta di vari giacimenti di gas naturale, nasce l’esigenza di adattare gli impianti funzionanti a Gas, all’utilizzo del metano, questo è l’input che spinge Polidoro a spostare lo studio e la ricerca sui bruciatori multigas.
Ad oggi Polidoro è fornitore di primaria importanza per la maggior parte dei costruttori europei di apparecchi da riscaldamento. Questo spiega la continua crescita di questa azienda che negli ultimi 4 anni ha avuto un innalzamento delle vendite del 60%.
SFIDA
La collaborazione tra Qaulitas Informatica e Polidoro inizia nel 1998, quando Polidoro implementa nel suo stabilimento NET@PRO per controllare l’avanzamento degli ordini e il prelievo dei componenti, in un primo reparto pilota. Valutata l’efficacia e i benefici che la soluzione Qualitas ha portato, Polidoro nel 2000 estende NET@PRO a tutto lo stabilimento per poi portare avanti una continua collaborazione che vede Qualitas come un partner fondamentale per il successo aziendale, tanto da scegliere ancora una volta NET@PRO come soluzione a due esigenze che Polidoro si trovava ad affrontare: la misurazione della produttività e la gestione della manutenzione.
L’ESIGENZA DI MISURAZIONE DELLA PRODUZIONE
Già dal 2006, Polidoro aveva intrapreso l’analisi degli indicatori di produzione che veniva gestita, da prima in versione cartacea con delle tabelle di produttività affisse nei vari reparti e successivamente utilizzando delle tabelle Excel e dei contatori. Queste soluzioni permettevano di avere una visione generale dei reparti sul rendimento delle persone dirette e sull’efficienza globale dell’azienda compresi gli indiretti, ma non permettevano agli operatori di avere sotto controllo l’andamento della produzione in tempo reale, inoltre la registrazione dei dati risultava particolarmente onerosa e i dati erano di natura troppo generale.
Si riscontrava anche la difficoltà di conoscere sistematicamente un dato oggettivo del tempo in cui la macchina è stata ferma e della reddittività della macchina in funzione e contemporaneamente si sentiva l’esigenza di capire se l’attenzione alla qualità potesse aver inciso negativamente nella produttività generale. Nasce quindi la necessità di poter misurare la produttività di ogni singola macchina direttamente nella stazione di lavoro dell’operatore e di poter regolare il tempo di lavorazione al takt time (tempo massimo permesso per produrre un prodotto in modo da soddisfare la domanda) della macchina.
LA GESTIONE PREVENTIVA DELLA MANUTENZIONE
Nel 2014, Polidoro si è trovata a fronteggiare l’aumento della produzione e l’esigenza di rifornire i clienti in tempi sempre più brevi e con qualità. Ciò a portato l’azienda a rivedere il concetto di pianificazione e controllo delle attività manutentive degli impianti produttivi. In un primo tempo, infatti, le operazioni di manutenzione preventiva degli impianti erano gestite attraverso checklist in tabelle excel, le richieste di intervento da parte dei reparti passavano attraverso supporti cartacei, si riscontava una mancanza di feedback sulle manutenzioni ai reparti e la registrazione degli interventi eseguiti era una operazione difficoltosa.
Diventa dunque necessario attuare degli interventi di manutenzione programmata e preventiva e ancora una volta Polidoro trova in una soluzione Qualitas Informatica la risposta alle proprie esigenze. Qualitas Informatica inizia così la realizzazione di un modulo ad hoc in grado di gestire un programma di manutenzione preventiva che riguarda 540 macchine.
SOLUZIONE
SOLUZIONE PER LA MISURAZIONE DELLA PRODUZIONE
Gli obiettivi che Qualitas si è posta per il cliente sono stati:
- creare uno strumento semplice, di facile lettura e comprensione per l’operatore;
- realizzare un indicatore che possa dare tutte le informazioni utili alla lavorazione e fruibili con immediatezza;
- fornire al capo reparto gli strumenti necessari ad individuare il grado di efficienza della lavorazione / impianto in modo immediato e semplice;
- fornire alla Direzione uno strumento di controllo e di dialogo con il Gemba semplice, di immediata lettura e non interpretabile.
Si è passati dunque all’implementazione in azienda di NET@PRO, attraverso il quale è stato possibile creare in un primo momento ANDON 1.0, che ha consentito la visualizzazione dei dati OEE (Overall Equipment Effectiveness) macchina e produttività istantanea e settimanale direttamente su schermo, oltre che la registrazione automatica dei dati. Ma rimanevano delle problematiche da risolvere: molti dati numerici da osservare sul medesimo schermo e nessuna registrazione delle fermate.
Grazie all’analisi di queste problematiche si è passati poi alla soluzione ANDON 2.0 attuata grazie a NET@PRO. Questa soluzione ha portato:
- visualizzazione della produttività istantanea giornaliera;
- visualizzazione dell’OEE istantaneo del turno;
- calcolo del ritardo per la registrazione delle fermate varie;
- visualizzazione delle varie fermate compreso il setup;
- semplicità di lettura.
I vantaggi derivati dall’adozione di ANDON 2.0 da parte della Polidoro SPA, non tardarono a farsi vedere: maggiore produttività degli impianti, dati precisi e sistematici, riduzione progressiva degli stop delle macchine dovuti ai guasti, miglioramento della gestione delle ore di produzione ed un risparmio effettivo di circa 35 ore settimanali per la registrazione dei dati.
SOLUZIONE PER LA GESTIONE PREVENTIVA DELLA MANUTENZIONE
Grazie a NET@PRO e all’integrazione con gli strumenti di misurazione della produttività è stato possibile:
Creare un unico strumento che contenga tutte le informazioni necessarie alla pianificazione della manutenzione
- Richieste dei reparti
- Piani di manutenzione preventiva
- Registrazione dei ricambi
- Integrazione con la programmazione della produzione
Creare una storia degli impianti produttivi
- Collegamento tra richieste e impianti
- Analisi degli interventi fatti e guasti accaduti
Standardizzare le manutenzioni
- Check list per la manutenzione preventiva
- Check list per l’auto manutenzione
Gestione dei fermi macchina per manutenzione preventiva NET@PRO Manutenzione viene gestito attraverso semplici interfacce per le richieste in grado di fornire informazioni sullo stato di avanzamento di ogni richiesta di manutenzione. Grazie a TPM è possibile visionare ogni richiesta, inserire delle note e aprire interventi di emergenza da parte degli addetti, da ogni PC presente in produzione. Il sistema è poi in grado di proporre automaticamente una serie di azioni da compiere per ogni singola parte con la possibilità di segnalare il risultato ottenuto, le richieste d’intervento possono essere automatiche e l’attività manutentiva può essere notificata via mail.
Infine, con il modulo TPM, è possibile gestire tutti i riepiloghi delle manutenzioni fatte (descrizione, nome di chi effettua l’intervento, tempi di esecuzione, note, ecc), oltre che i piani di manutenzione preventiva, auto manutenzione, suddivisione degli impianti in sotto parti e avere il riepilogo delle manutenzioni fatte con descrizione della richiesta, nome di chi ha fatto il lavoro, tempi di esecuzione e note
RISULTATO
SOLUZIONE PER LA MISURAZIONE DELLA PRODUZIONE
- Risparmio mensile di circa 35 ore impiegate per la registrazione dei dati
- +5% Produttività
- Miglioramento della gestione delle ore produttive
- Precisione e sistematicità del dato
- Riduzione progressiva delle ore di guasto (aumentano le attività di problem solving)
SOLUZIONE PER LA GESTIONE PREVENTIVA DELLA MANUTENZIONE
- Risparmio per il 2015 di 381 ore di registrazione dati
- Veritiera rilevazione delle ore di manutenzione per macchina
- Semplicita’ di analisi dei dati raccolti
- Azioni di miglioramento mirate all’effettivo problema
CONTRIBUTO DI:
RENATO DE FAVERI – RESP. SISTEMI INFORMATIVI
Implementando il MES NET@PRO di Qualitas Informatica siamo riusciti a migliore significativamente il livello di automatizzazione ed informatizzazione dei nostri processi in reparto confezionamento ottenendo importanti risultati, in particolare in termini di efficienza, controllo e velocità. Tutto ciò conservando uella flessibilità e rapidità di adattamento nei processi produttivi che sono per noi elementi strategici, che permettono di mantenere nei nostri prodotti la naturalità, freschezza e qualità artigianale che ci distingue.
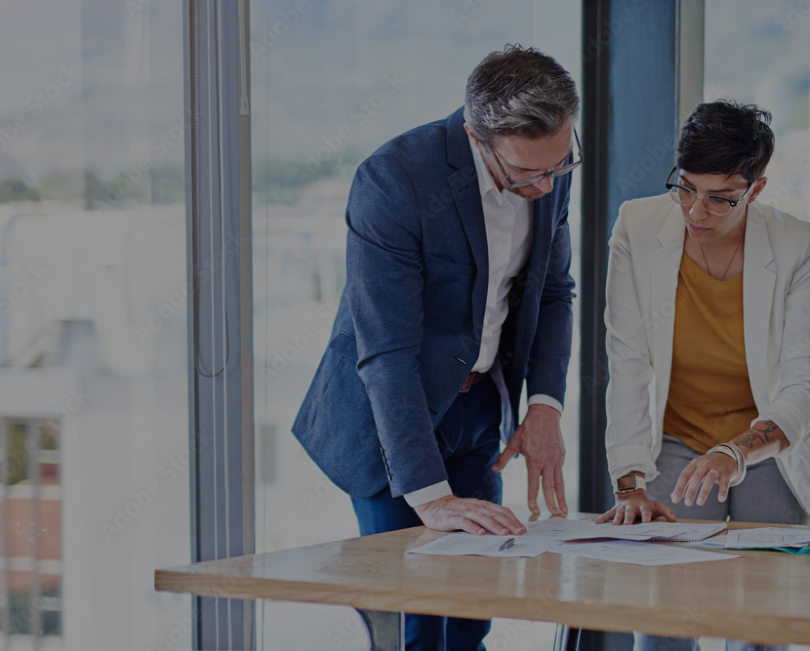
Leggi gli articoli del nostro blog
.png?width=810&height=651&name=Rectangle%2067%20(1).png)